Plasma etching and pyrolysis contribute to size reduction of laser polymerized 3D structures
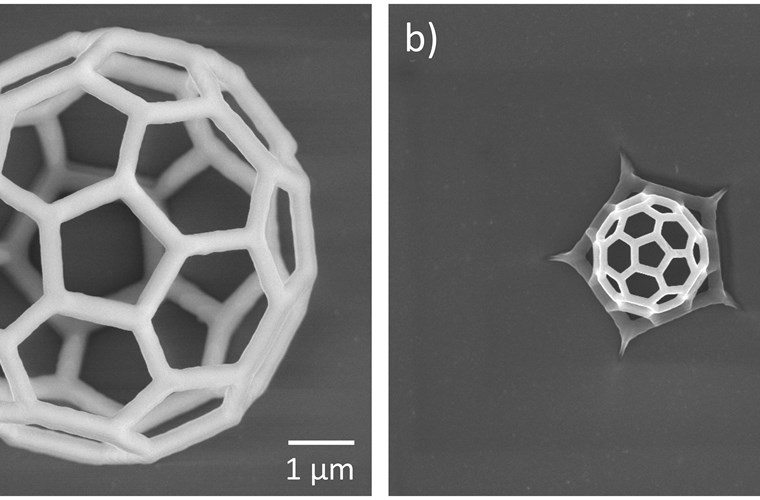
Researchers within NFFA Europe develop processes enabling fabrication of sub 100 nm smallest features sizes in free form 3D structures.
From JRA2 -High precision Manufacturing
Three-dimensional (3D) printing has become a thriving field over the last decades. Possibility to print 3D objects on demand seems to be so alluring that even home users are starting to own 3D printers. High tech industries as well as scientists working in different fields are not an exemption. Their interests in fast prototyping and microscale objects drive the development of 3D printing methods to meet the needs of resolution, throughput and printable materials.
3D structure with sub-100 nm features: top (a) and 45 degree tilt (b) views.
Laser polymerization has emerged as a direct writing technique allowing the fabrication of complex 3D structures with microscale resolution. The technique provides rapid prototyping capabilities for a broad range of applications from micro-optical elements in photonics to micro-scaffolds for cell studies in biology. Nonetheless, to meet the growing scientific interest in 3D nanoscale structures the resolution limits need to be pushed beyond the 100 nm benchmark, which is challenging in practical implementations. As a possible path towards this goal, plasma and heat treatment procedures of laser polymerized structures have been developed within NFFA Europe.
Most of the resins used to create 3D structures have some part of organic constituents in their composition. It has been demonstrated before that pyrolysis can be used to efficiently downscale 3D printed structures. During the process, polymerized structures are kept at elevated temperatures in an inert atmosphere. The high temperature causes organic molecules to break and produce some volatile products. This leads to a mass loss and rearrangement of the material making the structures to shrink. The degree of shrinkage depends on the resist material; the size can be reduced almost 5 times using commercially available materials.
“The smallest achievable feature sizes are mostly limited by the mechanical stability of the polymerized resist and the geometry of 3D structure”
– G. Seniutinas, postdoctoral researcher at PSI.
However, pyrolysis does not leave much freedom of changing the dimensions of the composing structural elements without impacting the size of the entire structure. To add this flexibility, an isotropic plasma etching of polymerized objects was developed within NFFA Europe. Highly isotropic oxygen plasma is used to thin down 3D structures in a controlled manner by attacking organic constituents of the resins. This procedure allows reduction of structural elements cross-sections and has a negligible effect on the overall size of the structure. Moreover, both treatment techniques can be combined to achieve feature sizes of 3D structures well below the 100 nm benchmark.
Downscaling of laser polymerized 3D structure: a) initial object; b) corresponding structure after pyrolysis. Size reduction of ~5 times can be achieved.
The developed techniques are available for users via NFFA transnational access platform and open new avenues to explore free form 3D structures at the nanoscale.
NFFA-EUROPE FACILITIES AND TECHNIQUES
Facilities:
Cleanroom at Paul Scherrer Institute, Switzerland & Laser laboratory at FORTH, Greece
Techniques:
Multiphoton laser polymerization (Nanoscribe Photonics Professional GT commercial system at PSI, in house built setup at FORTH); Isotropic oxygen plasma etching (BMP parallel plate etcher at PSI) & Pyrolysis (tube furnace at PSI).
For more information:
Dr. Gediminas Seniutinas, gediminas.seniutinas@psi.ch, Dr. Christian David, christian.david@psi.ch, ODRA, PSI Ost, Paul Scherrer Institut, Villigen PSI, 5232, Switzerland